国内制造企业如何融入增材制造的设计?
需要提及的是,当前现有的DfAM思维培训中,基本都绕不开仿真设计环节,但对于很多中小企业来说,花费巨资购买仿真软件以及花很长时间培养具备仿真能力的设计人员,并不是企业最好的选择,这也给这个技术的推广设置了巨大的门槛。以下两点可以帮助企业设计师快速获得DfAM思维能力,而不需要花费巨资。
1. 选择具备仿真能力的软件做基础仿真。
有一点必须注意的是:对于很多产品更重要的是能够制造出来,仿真只是帮助产品优化的手段之一,而对于一些本身结构优化要求不高,更多追求功能实现的产品设计来说,如果在仿真方面花费的时间与精力占用了产品太多的开发周期,并不可取。像Solidworks这样的上手容易的建模软件其实也有仿真功能,在网上寻找网课,只需要花费很少的费用和时间,学学基本的增加载荷做受力分析,就可以验证自己改造的设计,结构受力是否合理。
另外值得一提的是:Altair的 inspire仿真软件,也可供普通设计人员使用,操作上去除了复杂的操作流程。笔者在安装完软件,3小时内就能够根据教程,摸索着完成了第一个仿真和优化的结构—桥梁支撑结构。在完成关键步骤后,等待电脑的自动计算,得到结构的仿真优化结果,以帮助自己调整设计。由于是增材制造,设计师也不需要太担心加工不了的问题。
笔者上手inspire软件3小时后的第一个仿真设计
2. 跨领域借鉴学习经验,提升兴趣。
3D打印制造赋予了设计师巨大的设计灵活性,设计师完全可以跨界学习。大量的吸收各行业的与自家产品类似的结构设计,将别人好的设计优化结构点运用到自己的产品设计中。比如法兰面的设计,对于局部结构减重设计,完全可以参考借鉴汽车或者航空航天领域当中的典型减重结构设计方法,大胆的运到到自家的产品设计中,如果自己没有把握,就使用具备基础仿真功能的软件做单个功能的受力仿真(而不是全部),验证自己的推测,单一功能的仿真,也不需要大量的计算资源和时间。设计师以此不断积累新的功能结构轻量化的案例,自然就能让自己的产品越来越轻量化,越来越适合于增材制造。当设计师真正感受到这种自由组合,不受限制的设计方式带来的快感以后,更有动力去主动深入研究对于自家产品的优化方法。一步一步的实现向增材制造设计思维—DfAM设计思维的转化。
法兰面典型“花瓣”减重设计结构
写到这里笔者简单总结一下上面内容阐述的方法:
1. 学习具有仿真功能的软件,掌握基本仿真能力,如果产品本身优化性要求不高,则优先考虑增材制造的新工艺要求,保证产品开发周期和生产质量,逐步迭代;
2. 跨行业领域学习别人做的局部单一功能设计结构,并结合自身产品参数做仿真验证;
3. 将积累的局部单一功能设计通过建模融合到现有产品设计中;
4. 不断积累与迭代自己的产品和积累设计功能结构设计,逐步实现向DfAM设计思维转化。
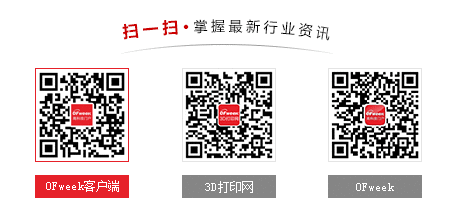
图片新闻
最新活动更多
-
7.30-8.1马上报名>>> 【展会】全数会 2025先进激光及工业光电展
-
即日-2025.8.1立即下载>> 《2024智能制造产业高端化、智能化、绿色化发展蓝皮书》
-
精彩回顾立即查看>> 2024(第五届)全球数字经济产业大会暨展览会
-
精彩回顾立即查看>> 《2024智能制造产业高端化、智能化、绿色化发展蓝皮书》
-
精彩回顾立即查看>> 全数会2024(第五届)中国智能制造数字化转型大会
-
精彩回顾立即查看>> Massivit大尺寸、超快速3D打印加速赋能教育创新需求
推荐专题
发表评论
请输入评论内容...
请输入评论/评论长度6~500个字
暂无评论
暂无评论